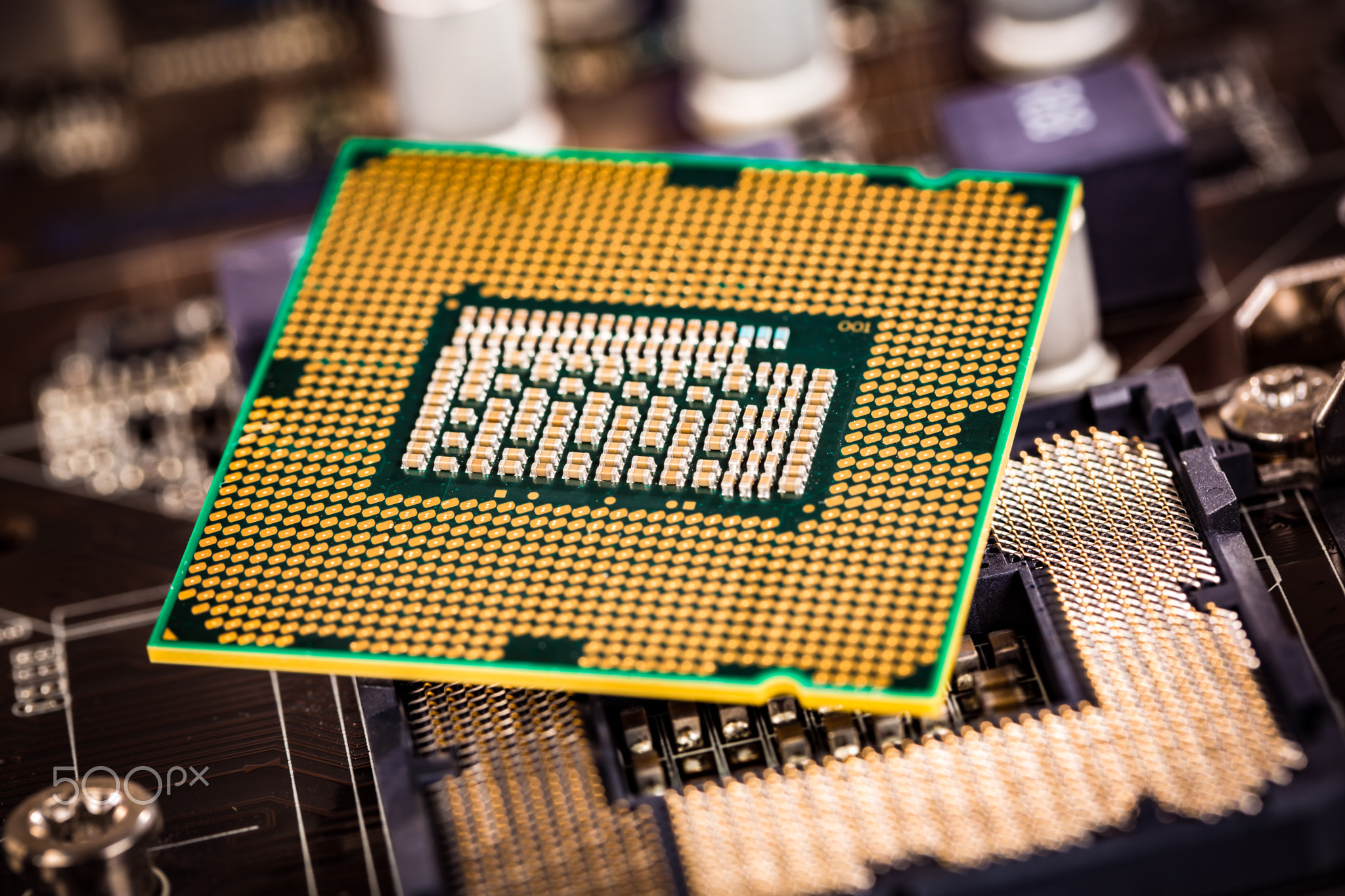
{"@context":"
https://schema.org/","@type":"Store","name":"ELECTRONIC COMPONENT SUPPLIER","image":[],"priceRange":"","servesCuisine":"","telephone":"+852-61807557","address":{"@type":"PostalAddress","streetAddress":"RM A1216, Flat A, 12/F. King Yip Factory Bldg","addressLocality":"nr 59 King Yip St. Kwun Tong, ","addressRegion":"Kowloon","postalCode":"59","addressCountry":"Hong Kong"}}
{Figure 13-9 {shows|exhibits|reveals} a bleed-off circuit at {rest|relaxation} with the pump {running|operating|working}. A needle valve’s inlet is teed right into a line going to the cylinder and its outlet is related to tank. The circuit only works with one actuator shifting at a time because all pump flow goes to the presently working function. Like a meter-in circuit, it only works with resistive hundreds as a outcome of it controls fluid into the actuator.|U-cups often use backup rings at pressures above 1500 psi to maintain them from extruding. All of the above cylinder-position indicators have one potential major flaw. If the half connected to the rod end will get disconnected for any cause, the machine still will cycle when the cylinder moves...although the disconnected load may be in the best way. If at all possible, mount limit switches on the machine member so its position is never misinterpreted.|Some purposes with excessive pace and heavy loads may need valves and limit switches to give enough time to convey the load to a smooth cease. Cushions add price on most cylinders so shouldn't be specified when pointless. For pneumatic cylinders, the standard working pressure is eighty psi although most vegetation cycle their air compressor between a hundred and fifteen to 125 psi. The purpose for the lower working strain is because line losses, particularly throughout high move surges, make it unimaginable to take care of compressor output pressure over the whole air provide system. One manufacturer has a modified rodless cylinder with a toothed belt and pulley arrangement to drive the workpiece attachment. It presents the option of an external output shaft to which a brake may be fitted to stop and maintain position.|This actuator sometimes has single driving gears or sprockets that produce the forces required for the push and pull motions. Pneumatic and hydraulic actuators are similar in that each use a fluid to channel the mechanical power and within the executions, terminology, electronic component test labs and parts. The two power circuits want a specific type of pump and a few valves for pressure and velocity control of the actuators.}
The cycle repeats until the solenoid is de-energized, which ends the cycle once the cylinder retracts. Pneumatic elements may be combined to cycle routinely without exterior controls (see schematic below). It exhibits compressed air managed by three valves (VLV05, VLV07 and VLV08).
Product Registration
You can subsequently remove the burden in similar increments and observe the flexibility of the rubber band to compress itself. Rubber bands, nevertheless, do not obey Hooke's Law perfectly subsequently as you unload, the rubber band shall be longer on the corresponding weights as you loaded. As previously talked about, on the point the place the fluid’s velocity is at its highest, the strain is at its lowest.
Ball screws or rack and pinion mechanisms on electrical actuators additionally act as a gear reduction ratio, so forces could be increased with sacrifice to hurry. Electric quarter-turn valve actuators are electro-mechanical units which are used to remotely control quarter-turn valves, corresponding to ball and butterfly valves. Compared to their pneumatic and hydraulic counterparts, electrical valve actuators present a more energy-efficient, clear, and quiet methodology of valve management. They could be purchased along with the valve as a bundle or as a separate unit and added onto an present quarter-turn valve. One line then supplies lubricated air and the other supplies non-lubricated air. The non-lubricated line feeds a second regulator that provides the electrically operated soft-start/dump valve (VLV02).
Br Quarter-turn Guide
Hydraulic systems often have a devoted power unit for every machine. They normally have a central power unit with pipes working to and from the presses out in the plant. Because these presses require no flow throughout their long closing instances, a single large pump can operate a number of of them. These hydraulic systems operate more like a compressed-air installation as a end result of the ability source is in a single location.