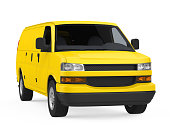
Introduction to Forklifts
Forklifts are an essential piece of equipment in a wide range of industrial and commercial settings. These versatile vehicles are designed to lift, move, and transport heavy loads and materials with ease. Forklifts play a crucial role in the efficient operation of warehouses, distribution centers, manufacturing facilities, construction sites, and many other environments where the movement of large or bulky items is a regular requirement.
The core function of a forklift is to use its load-bearing forks to pick up, carry, and place pallets, crates, boxes, and other types of packaged goods. This allows for the safe and controlled transportation of materials that would otherwise be difficult or dangerous for workers to move manually. Beyond just
material handling sale industrial equipment handling, forklifts also enable the strategic positioning and stacking of inventory, allowing for optimal space utilization within a facility.
With a wide range of forklift models, designs, and capabilities available, organizations can select the specific type of forklift that best matches their operational needs and work environments. From compact electric models for indoor use to robust, all-terrain units for outdoor jobsites, the forklift marketplace offers solutions to fit a diverse array of materials handling requirements.
The Anatomy of a Forklift
At the core of every forklift is its load-carrying mechanism - the forks. These tines, typically made of sturdy steel, extend from the front of the forklift and are used to pick up and transport pallets, crates, or other packaged goods. The height to which the forks can be raised is controlled by the forklift's mast - the vertical assembly that raises and lowers the load.
To provide the necessary power and stability for lifting and moving heavy loads, forklifts are equipped with a counterweight at the rear of the vehicle. This counterweight, often made of cast iron or steel, serves to balance out the weight of the load being carried in the front, preventing the forklift from tipping over.
The forklift's power source is another key component, with models available that are powered by internal combustion engines (fueled by gasoline, diesel, or propane) or by rechargeable electric batteries. Internal combustion forklifts are well-suited for outdoor use and heavy-duty applications, while electric forklifts excel in indoor environments, offering quieter operation and zero direct emissions.
Other essential forklift features include:
- Steering mechanism and wheels/tires
- Operator controls and instrumentation
- Safety systems like seatbelts and overhead guards
- Hydraulic systems for lifting and tilting the forks
- Brakes and suspension for safe maneuvering
The specific configuration and capabilities of a forklift are determined by its intended application and the unique requirements of the work environment.
Forklift Classifications and Types
Forklifts come in a wide variety of models and designs to accommodate diverse materials handling needs. The major forklift classifications include:
Counterbalance Forklifts
The most common type of forklift, counterbalance models use the weight of the vehicle's counterweight to offset the load being carried at the front. These forklifts are well-suited for standard pallet and crate handling in warehouses, distribution centers, and manufacturing facilities.
Reach Forklifts
Designed for
narrow-aisle applications, reach forklifts have an extendable mast that allows the forks to reach farther into racking systems. This makes them ideal for high-density storage environments where space is limited.
Rough Terrain Forklifts
Built to handle uneven surfaces, rough terrain forklifts are typically powered by diesel engines and feature large, durable tires. These models are commonly used on construction sites, in quarries, and in other outdoor settings with challenging ground conditions.
Order Picker Forklifts
Also known as elevated work platforms, order pickers lift the operator as well as the load, allowing the user to directly access items on tall storage racks. These specialized forklifts are valuable in applications that require frequent picking and replenishment of inventory.
Pallet Jacks and Stackers
While not considered full forklifts, pallet jacks and stackers are materials
material handling usa industrial equipment tools that serve as compact, manual alternatives. Pallet jacks are used to move pallets short distances, while stackers can lift and stack pallets to a limited height.
Electric Forklifts
Powered by rechargeable batteries rather than internal combustion engines, electric forklifts offer numerous advantages, including quiet operation, zero direct emissions, and lower maintenance requirements. These models are well-suited for indoor applications where emissions and noise are a concern.
The specific forklift model selected for a given application will depend on factors such as load capacity, lift height, maneuverability, power source, and environmental conditions. Consulting with forklift dealers and materials handling experts can help organizations determine the optimal equipment for their needs.
Forklift Safety and Regulations
Operating a forklift requires specialized training and certification, as these vehicles pose significant safety risks if not handled properly. Forklift operators must be aware of and adhere to a range of safety protocols and regulations to protect themselves, their co-workers, and the materials they are transporting.
Key forklift safety considerations include:
Operator Training and Certification
In the United States, the Occupational Safety and Health Administration (OSHA) mandates that all forklift operators receive proper training and evaluation before being authorized to use the equipment. This training covers topics such as vehicle handling, load capacity, and workplace-specific hazards.
Stability and Load Capacity
Forklifts are designed to handle specific maximum load capacities, which vary by model. Exceeding these limits can compromise the vehicle's stability and lead to tip-overs or dropped loads. Operators must be aware of and strictly adhere to the forklift's load rating.
Visibility and Clearance
Forklift operators must maintain clear visibility of their surroundings to avoid collisions with people, objects, or infrastructure. Forklifts are also required to have adequate overhead and front-end clearance to prevent the load or mast from striking ceilings, doorways, or racking systems.
Pedestrian Safety
In busy industrial environments, forklift operations pose a significant risk to on-foot workers. Forklifts must yield the right-of-way to pedestrians, and operators must be vigilant in watching for and responding to the presence of workers in their vicinity.
Maintenance and Inspections
Regular inspections, maintenance, and repair of forklifts are essential for ensuring the vehicles remain in safe, working condition. OSHA requires pre-shift inspections by operators, as well as periodic professional maintenance by qualified technicians.
In addition to OSHA regulations, many states and local jurisdictions have their own forklift safety laws and requirements. Successful forklift operations depend on a comprehensive safety program that encompasses operator training, equipment maintenance, and strict adherence to all relevant regulations.
The Forklift Marketplace and Purchasing Considerations
Forklifts can represent a significant capital investment for organizations, with new models typically ranging from $20,000 to $50,000 or more, depending on the vehicle's capabilities and features. Used and refurbished forklifts are also available on the secondary market, often at lower price points.