Straddle milling is often used to design a sq. or hexagonal surfaces. It is used to mill flat surfaces that are neither parallel nor perpendicular to the axis of the milling cutter. It is often known as angle milling. The one-angle milling cutter is used to perform this operation. Angular milling is the operation of producing an angular surface on a workpiece apart from at right angles of the axis of the milling machine spindle. An angular groove could also be single or double angle and may be of varying included angle based on the type and contour of the angular cutter used. This case will be improved by growing feed, фрезерный станок lowering speed, and using unequal pitch cutters. Chip clogging: The milling machine also suffers from the issue of chip clogging which may be decreased through the use of lowering the number of teeth on the cutter and rising speed and chip pockets. That is all about Milling machines.
The software holder is mounted on the cross slide. Hence, you'll be able to move it alongside the longitudinal or lateral axis of the lathe machine. The mixed movement, alternatively, allows you to achieve the specified machining operation. You'll be able to configure the device put up on a metallic lathe machine into 4 totally different settings: single screw, open facet, four bolt, and four-manner. Gang instrument lathes, on the other hand, have particular tool posts to hold multiple reducing tools for a distinct machining course of. The apron is coupled with the feed rod on the carriage for computerized motion. Every part has a devoted hand wheel that you could rotate. An bizarre lathe machine could contain up to three hand wheels, which control the carriage, tailstock, and slicing software. The chuck is a work-holding machine utilized in mounting workpieces having distinct diameters. It significantly holds these with a short length and enormous diameter and those with irregular shapes. But for a CNC lathe, a hydraulic chuck is used. A thread is a uniform spiral groove with a specific size and pitch. Deeper threads require multiple passes of a instrument. The knurling process creates serrated patterns on the surface of a part. Knurling will increase the gripping friction and the visual look of the machined half. This machining process makes use of a unique software made up of one or more cylindrical wheels (knurls) that may rotate within the instrument holders. The knurls comprise teeth which are rolled against the floor of the workpiece to kind serrated patterns. The commonest knurled nib is a diamond sample. When boring, a device penetrates the workpiece axially and removes material alongside the inside floor to either create completely different shapes or to enlarge an existing gap. Through the drilling process, the material is removed from the inside of a workpiece.
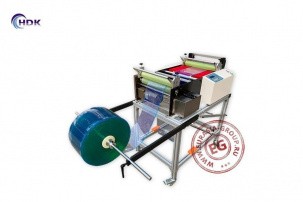
Ensure precision metal shaping and metalworking with this eight x sixteen metal lathe. It is a beneficial addition to any workshop since it options a versatile speed management system. Its strong development keeps it intact to ensure its sturdiness for the long run. With a simple and clear interface, this lathe is super easy to function. Lathe Diagram - How it really works? The following diagram explains the fundamental working principle of the machine. Major specifications of your lathe are, the utmost distance between the stay and lifeless center and the peak of the middle over the guideways and carriage. The primary one indicates the maximum length of labor which you can flip and the second (A and B in the sketch) indicates the maximum diameter which you can swing/ revolve safely over the guideways and carriage. Now it is time for us to continue our exploration and achieve some information concerning the different types of Lathe Machines and their utility, professionals and cons. Right here is the checklist of 12 frequent sorts of lathes which can be most generally utilized in wooden and metallic working industries. 1. Wooden Turning Lathe. 9. Vertical Turret Lathes. 2. Pace Lathe. 10. Special Objective Lathes. 2. Crankshaft Turning Lathe.
CNC milling machines are used to exactly and precisely cut the material. It is feasible to provide just about any item and element with a CNC milling machine, as the machine can minimize a large number of shapes and angles. There are several different types of milling machines. A few of them embody column and knee sort, plain or horizontal, vertical, universal, fixed mattress sort, simplex, duplex, triplex, planer kind, rotary table, drum type, profile milling, planetary sort, tracer operated, pantograph sort, and CNC milling machine. Milling machines primarily fall into two types primarily based on the orientation of the primary spindle: horizontal and vertical. Vertical milling machines are used for plunge cuts and drilling, while horizontal milling machines carry out tasks requiring specific heavy-duty machining. Each varieties use rotating cutting instruments (end mills, mattress mills, face mills, drills, and many others.) spinning at speeds as much as 20,000 RPM. Nuts, bolts, piston, Ram, pump half, electric motor parts, sleeves, Air craft components, gun barrels, candlesticks, prepare parts, cue sticks, wooden bowls, baseball bat, crankshaft and many more things. Engine Lathe or heart Lathe. Engine lathe is a very powerful tool in the Lathe family and by far the most generally used type of Lathe machine. Its name is derived from the truth that early machine tools had been pushed by separate Engines or central engine with overhead belt and shafts. The operations which may be performed by the Engine Lathe machine are Turning, going through, grooving, knurling, threading, and lots of more operations will be carried out by it. Engine lathe include headstock, Tailstock, mattress, saddle, carriage and other elements.